- Регистрация
- 26.06.2019
- Сообщения
- 109
- Реакции
- 52
- Баллы
- 98
- Город
- Н.Новгород
- Имя
- Сергей
Приветствую, товарищи! Вот решил поделиться своими страданиями вокруг станка, которому посвящен данный форум. Напомню, ко мне пришел станок с убогим удешевленным профилем, который имеет более тонкую силовую конструкцию. Надо было отправить это все обратно китайцам, но мне не терпелось запустить станок и я его таки собрал до того как начал ругаться с продавцом, ну да ладно, приступим.
После сборки и проверки работоспособности выяснилось что жесткости у станка нет, вообще поразила способность китайцев экономить на спичках - нет никаких укрепляющих конструкцию элементов, кроме классических уголков. Даже винты поскупились закрутить по торцам рамы, что уже было бы неплохо. Фактически станок можно было скрутить руками и это печалило.
Сразу пришла идея обшить чем-то станок для придания ему большей жесткости. Листовой алюминий я пожалел, обрезки бакелизированной фанеры также решил припасти для следующего уже полностью самопального станка. Выбор пал на обрезки ламината толщиной 10мм, что по сути своей есть МДФ. Материал довольно мягкий, но хорошо держит деформацию вдоль плоскости.
Ламинат порезал ручной ножовкой с коррекцией рубанком и наждачкой, по сути делал на коленке. Пришил вдоль осей Х и У на винты М4 и гайки для профиля, которые некогда покупал в запас для 3D-принтера. Уже на данном этапе станок обрел уверенность в завтрашнем дне, перестал играть при попытках скручивания руками.
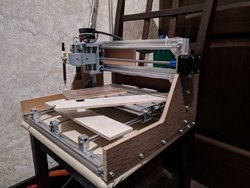
Днище решил укрепить обрезком кухонной дешманской столешницы толщиной 38мм, она конечно рыхловата, но плоскость держит довольно хорошо. Ее пришил на винты М5 и 8 гаек, которые были взяты из излишков, оставшихся после сборки, также высвобожденных из-под уголков или моторов.
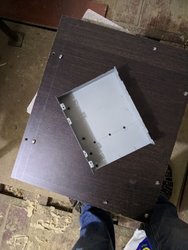
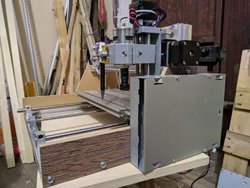
Моторы по ХУ тоже пришлось модифицировать, винты, соединяющие мотор и крепежную пластину оказались очень короткими, я умудрился сорвать резьбу на одном из креплений. Решение - покупка винтов М3х40 и самоконтрящихся гаек(в моем случае из нержавейки). Старые винты попарно по диагонали выкрутил, закрутил купленные, они прошли мотор насквозь, вышли как раз на необходимое для крепления расстояние. И пластина крепилась уже гайками. Но эти гайки упирались в крепления валов оси Х и пришлось менять крепление мотора, в связи с чем освободилась пара гаек.
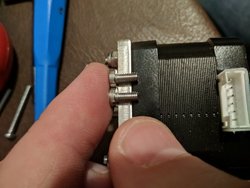
Извиняюсь за это лирическое отступление, возвращаемся к раме.
В общем, гаек было 8, на столько и закрепил, по две точки крепления около стыка вертикальных профилей с основанием и по две под каждым креплением вала оси У. Два лишних отверстия - это мой классический косяк, забыл что отрезал столешку с запасом. Пилил столешницу циркуляркой по шаблону - обрезку фанеры с ровным краем - нанотехнологии!
Также пришла в голову идея использовать корпус от старого DVD-rom'а в качестве корпуса для платы управления. И пришил я его сбоку, там где торчит мотор оси Х, пространство за осью решил оставить для блока питания или чего-то еще на будущее.
"И увидел он, что это было хорошо..." и решил не останавливаться. Решил добавить еще плашку вдоль оси Х, параллельно основанию, а следом за ней решил вообще наглухо закрыть тыл станка, потеряв несколько миллиметров рабочей зоны и возможность подсовывать длинные заготовки. Но если надо - потом выпилю дупло для этого. Материал фанера сорта ФК 15мм. Естественно, задник был стянут со всеми примыкающими элементами саморезами и придал конструкции максимальную для данного варианта жесткость и законченный "дедовский" вид. Больше по части укрепления конструкции я ничего делать не планирую.
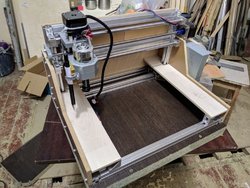
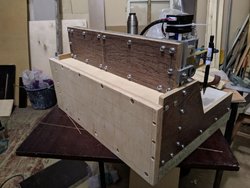
Также я выпилил планки которые должны заходить под стол и частично защищать от пыли направляющие, но сейчас они под вопросом, потому как появилась идея сделать это иначе. Изначально я планировал использовать подобие "гармошки" для защиты от пыли, но пообщавшись со станком понял, что это не вариант.
Помимо этого я сделал и проверил z-щуп с опторазвязкой по аналогии с приведенной на форуме схемой, только чисто на оптроне без логики. Концевики буду ставить б/у также с опторазвязкой, фильтр от помех также из б/у компонентов. Вообще я рад что хоть что-то из того, что я выпаивал ранее из оргтехники начинает пригождаться.
Сделал черновой вариант держателя карандаша, но еще в работе не пробовал.
Сейчас станок разобран по части оси У, т.к. мотор переезжает на соседний профиль, а крепление ходовой гайки к столу переезжает на край столика(понимаю, что по центру лучше, но куда деваться). Также надо разработать и напечатать крепление для опорного подшипника для винта, составленного из двух, т.к. они есть, и применить на оси У алюминиевую муфту-пружинку, оставшуюся от оси Z принтера.
Столик родной выправил струбцинами примерно до кривизны в 0.5мм, но можно еще над ним попыхтеть. Также сделал скромный жертвенник. Сразу вопрос опытным пользователям подобных столов - не выпадают ли гайки от вибрации, стоит ли залить их каким-то клеем с обратной стороны?
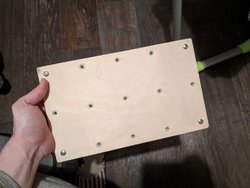
Вот тему буду пополнять по мере поступления новостей. Извиняюсь, что проект не завершен, просто зная себя, лучше я опишу это сейчас так, чем потом будет лень вспоминать что да как.
Также жду конструктивную критику и рекомендации с пониманием сути модернизации "из того что было". В частности меня интересуют последствия переезда точки крепления ходовой гайки к столу из центра к краю. Не будет ли подклинивать?
Пока затраты составляют примерно 600 рублей с учетом бесплатности обрезков и имеющегося инструмента.
Финальная возможная перспектива данного проекта - превращение cnc3018 в cnc1512 с введением третьей опоры для валов посередине осей ХУ с соответствующим расширением кареток, в т.ч. с целью установки двух-трех инструментов с пылеотведением.
Как-то так, получилось много букв, ну да ладно, может кому пригодится...
После сборки и проверки работоспособности выяснилось что жесткости у станка нет, вообще поразила способность китайцев экономить на спичках - нет никаких укрепляющих конструкцию элементов, кроме классических уголков. Даже винты поскупились закрутить по торцам рамы, что уже было бы неплохо. Фактически станок можно было скрутить руками и это печалило.
Сразу пришла идея обшить чем-то станок для придания ему большей жесткости. Листовой алюминий я пожалел, обрезки бакелизированной фанеры также решил припасти для следующего уже полностью самопального станка. Выбор пал на обрезки ламината толщиной 10мм, что по сути своей есть МДФ. Материал довольно мягкий, но хорошо держит деформацию вдоль плоскости.
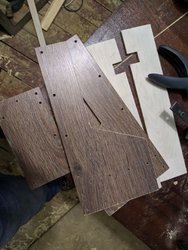
Ламинат порезал ручной ножовкой с коррекцией рубанком и наждачкой, по сути делал на коленке. Пришил вдоль осей Х и У на винты М4 и гайки для профиля, которые некогда покупал в запас для 3D-принтера. Уже на данном этапе станок обрел уверенность в завтрашнем дне, перестал играть при попытках скручивания руками.
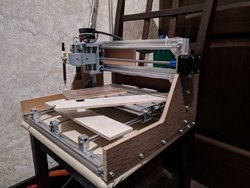
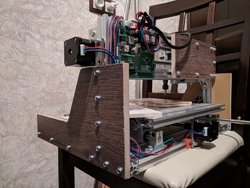
Днище решил укрепить обрезком кухонной дешманской столешницы толщиной 38мм, она конечно рыхловата, но плоскость держит довольно хорошо. Ее пришил на винты М5 и 8 гаек, которые были взяты из излишков, оставшихся после сборки, также высвобожденных из-под уголков или моторов.
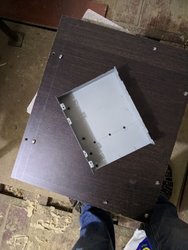
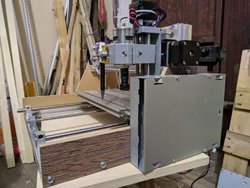
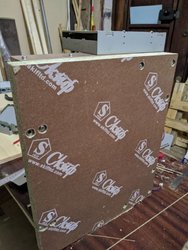
Моторы по ХУ тоже пришлось модифицировать, винты, соединяющие мотор и крепежную пластину оказались очень короткими, я умудрился сорвать резьбу на одном из креплений. Решение - покупка винтов М3х40 и самоконтрящихся гаек(в моем случае из нержавейки). Старые винты попарно по диагонали выкрутил, закрутил купленные, они прошли мотор насквозь, вышли как раз на необходимое для крепления расстояние. И пластина крепилась уже гайками. Но эти гайки упирались в крепления валов оси Х и пришлось менять крепление мотора, в связи с чем освободилась пара гаек.
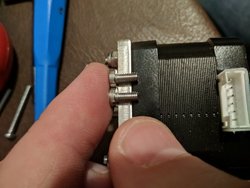
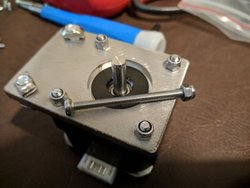
Извиняюсь за это лирическое отступление, возвращаемся к раме.
В общем, гаек было 8, на столько и закрепил, по две точки крепления около стыка вертикальных профилей с основанием и по две под каждым креплением вала оси У. Два лишних отверстия - это мой классический косяк, забыл что отрезал столешку с запасом. Пилил столешницу циркуляркой по шаблону - обрезку фанеры с ровным краем - нанотехнологии!
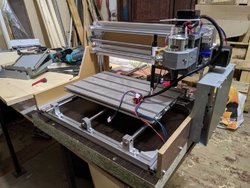
"И увидел он, что это было хорошо..." и решил не останавливаться. Решил добавить еще плашку вдоль оси Х, параллельно основанию, а следом за ней решил вообще наглухо закрыть тыл станка, потеряв несколько миллиметров рабочей зоны и возможность подсовывать длинные заготовки. Но если надо - потом выпилю дупло для этого. Материал фанера сорта ФК 15мм. Естественно, задник был стянут со всеми примыкающими элементами саморезами и придал конструкции максимальную для данного варианта жесткость и законченный "дедовский" вид. Больше по части укрепления конструкции я ничего делать не планирую.
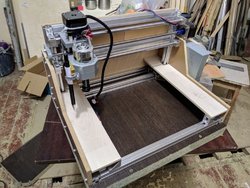
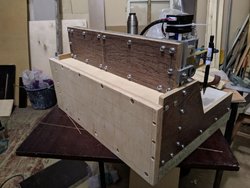
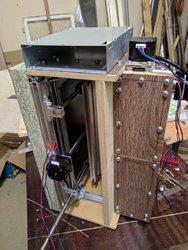
Также я выпилил планки которые должны заходить под стол и частично защищать от пыли направляющие, но сейчас они под вопросом, потому как появилась идея сделать это иначе. Изначально я планировал использовать подобие "гармошки" для защиты от пыли, но пообщавшись со станком понял, что это не вариант.
Помимо этого я сделал и проверил z-щуп с опторазвязкой по аналогии с приведенной на форуме схемой, только чисто на оптроне без логики. Концевики буду ставить б/у также с опторазвязкой, фильтр от помех также из б/у компонентов. Вообще я рад что хоть что-то из того, что я выпаивал ранее из оргтехники начинает пригождаться.
Сейчас станок разобран по части оси У, т.к. мотор переезжает на соседний профиль, а крепление ходовой гайки к столу переезжает на край столика(понимаю, что по центру лучше, но куда деваться). Также надо разработать и напечатать крепление для опорного подшипника для винта, составленного из двух, т.к. они есть, и применить на оси У алюминиевую муфту-пружинку, оставшуюся от оси Z принтера.
Столик родной выправил струбцинами примерно до кривизны в 0.5мм, но можно еще над ним попыхтеть. Также сделал скромный жертвенник. Сразу вопрос опытным пользователям подобных столов - не выпадают ли гайки от вибрации, стоит ли залить их каким-то клеем с обратной стороны?
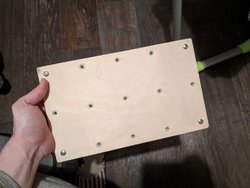
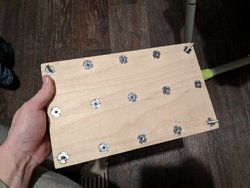
Вот тему буду пополнять по мере поступления новостей. Извиняюсь, что проект не завершен, просто зная себя, лучше я опишу это сейчас так, чем потом будет лень вспоминать что да как.
Также жду конструктивную критику и рекомендации с пониманием сути модернизации "из того что было". В частности меня интересуют последствия переезда точки крепления ходовой гайки к столу из центра к краю. Не будет ли подклинивать?
Пока затраты составляют примерно 600 рублей с учетом бесплатности обрезков и имеющегося инструмента.
Финальная возможная перспектива данного проекта - превращение cnc3018 в cnc1512 с введением третьей опоры для валов посередине осей ХУ с соответствующим расширением кареток, в т.ч. с целью установки двух-трех инструментов с пылеотведением.
Как-то так, получилось много букв, ну да ладно, может кому пригодится...