- Регистрация
- 25.12.2019
- Сообщения
- 153
- Реакции
- 106
- Баллы
- 63
- Город
- Москва
-
Рекомендованный
- #1
Приветствую всех!
Поработал какое-то время на стоковом 3018. Т.к. был совсем не в теме, то это дало некоторый опыт. Обрабатывал мелкие детали в основном из поликарбоната. Пробовал люминь, но станок колбасило сильно. Самое раздражающие - болтанка шпинделя из-за валов оси Z. Приложив пальцем нагрузку к концу шпинделя килограмм в 5, его можно отвести, наверное, на пол мм в сторону. Да и на пластике поверхность ребристая получалась - нужно было работать много шкуркой.
Сейчас, вооружившись статьей с данного форума (очень огромная благодарность создателю!
), начал переделывать свой.
Единственное, профили не стал использовать 40х20 - мне показались они хлипкие. В основание поставил 40х40, большей частью из-за этого:
Место 1 выглядит покрепе, чем место 1. были даже мысли укрепить место 2 напротив креплений рельс (через гайки крепкие пластины притянуть).
Плюс нагрузки есть и боковые, не малые, потому ширина будет только в плюс жесткости.
Получилось так:
Соответственно, вместо винтов DIN912 с внешней стороны пришлось использовать обычные болты.
Проставку под держатель гаек сделал временно (теперь вижу, что постоянно
) из этого же профиля - даже отрезать не пришлось, до этого отрезал кусок на пробу совершенно случайно нужной толщины:
Думал о ШВП 1204, но решил, что слишком много переделок, причем там неизвестно какой люфт, а тут его можно выбрать (на фото еще нет винтов в гайке). Да и ручки со стандартной разделкой концов сохранить не получится. (Кстати, поставив только лишь винты на оси X и Y, заметил улучшение поверхности резки.)
Сразу сделал защиту, чтобы не запачкивались направляющие.
Рулон (когда защита крепится к столу с 2х сторон, и проходит через ролики спереди и позади основания) не стал делать, т.к. постоянно пользуюсь ручками ручной подачи, а рулон их перекроет - придется выносить через ремни. Да и нужно было сделать срочно из подручных материалов:
Гофра с али 300 мм шириной (недешевая, кстати, вещь), алюминиевая трубка ф10х1, и распечатанные детали. Сделано так, чтобы с любой стороны просто вынималось, без использования каких-либо инструментов. Трубки сделаны для того, чтобы, с одной стороны, в крайних положениях стол не упирался в защиту ( а сама сложенная гофра тоже порядка 10 мм), а с другой - чтобы выдвинутая гофра не перекрывала ручку подачи. То есть край гофры отодвигается столом, если надо, но когда не надо, не выходит за пределы станины. По фото должно быть понятно:
(К столу крепление забыл сфоткать). Посмотрим, как себя поведет. Но пока (после пластика) внутри все чисто. Снять и обслужить (смазать каретки) тоже легко.
Для оси Х (на портале) планирую использовать такой профиль:
Профили использую соберизаводовские, т.к. рельсы mgn12ложатся на ребра, а не висят на краях паза.
Но вот теперь возникли вопросы. Самый первый: Ось Х будет делаться после оси Z. Захотелось попробовать шпиндель с водяным охлаждением, но они все от 800 Вт.Сможет ли родной движок таскать эту массу нормально, или оно повлечет изменение и этой части? Не хотелось бы из этого станка собирать полностью другой, но с недостатками этого. На форуме не нашел, но есть упоминания о том, что ставили такие (мое сообщение стерли в одной из тем, как не относящееся). Если есть, буду благодарен на ссылки на форуме/ютубе/просто текстом. Интересует так же шумность на 12-15 тыс. оборотах по сравнению с воздушником.
Второй. Если использовать шпиндель 800 Вт ф65 мм, это приведет к уменьшению рабочего поля по Х. Вот есть мысль, по краям (где крепятся стойки портала) к профилю 40х40 прикрутить профиль 40х20, и уже через него крепить стойки. Поле сохранится, а жесткость? Вероятно. Как думаете, стоит морочиться, или забить?
Поработал какое-то время на стоковом 3018. Т.к. был совсем не в теме, то это дало некоторый опыт. Обрабатывал мелкие детали в основном из поликарбоната. Пробовал люминь, но станок колбасило сильно. Самое раздражающие - болтанка шпинделя из-за валов оси Z. Приложив пальцем нагрузку к концу шпинделя килограмм в 5, его можно отвести, наверное, на пол мм в сторону. Да и на пластике поверхность ребристая получалась - нужно было работать много шкуркой.
Сейчас, вооружившись статьей с данного форума (очень огромная благодарность создателю!
Единственное, профили не стал использовать 40х20 - мне показались они хлипкие. В основание поставил 40х40, большей частью из-за этого:
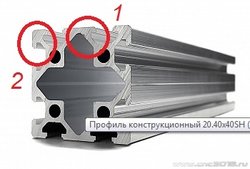
Место 1 выглядит покрепе, чем место 1. были даже мысли укрепить место 2 напротив креплений рельс (через гайки крепкие пластины притянуть).
Плюс нагрузки есть и боковые, не малые, потому ширина будет только в плюс жесткости.
Получилось так:
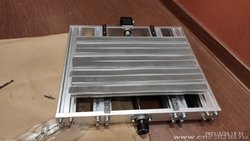
Соответственно, вместо винтов DIN912 с внешней стороны пришлось использовать обычные болты.
Проставку под держатель гаек сделал временно (теперь вижу, что постоянно
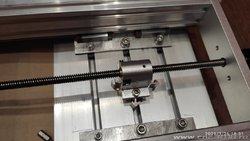
Думал о ШВП 1204, но решил, что слишком много переделок, причем там неизвестно какой люфт, а тут его можно выбрать (на фото еще нет винтов в гайке). Да и ручки со стандартной разделкой концов сохранить не получится. (Кстати, поставив только лишь винты на оси X и Y, заметил улучшение поверхности резки.)
Сразу сделал защиту, чтобы не запачкивались направляющие.
Рулон (когда защита крепится к столу с 2х сторон, и проходит через ролики спереди и позади основания) не стал делать, т.к. постоянно пользуюсь ручками ручной подачи, а рулон их перекроет - придется выносить через ремни. Да и нужно было сделать срочно из подручных материалов:
Гофра с али 300 мм шириной (недешевая, кстати, вещь), алюминиевая трубка ф10х1, и распечатанные детали. Сделано так, чтобы с любой стороны просто вынималось, без использования каких-либо инструментов. Трубки сделаны для того, чтобы, с одной стороны, в крайних положениях стол не упирался в защиту ( а сама сложенная гофра тоже порядка 10 мм), а с другой - чтобы выдвинутая гофра не перекрывала ручку подачи. То есть край гофры отодвигается столом, если надо, но когда не надо, не выходит за пределы станины. По фото должно быть понятно:
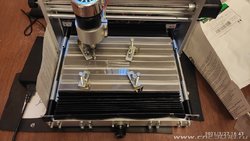
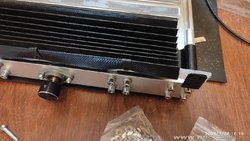
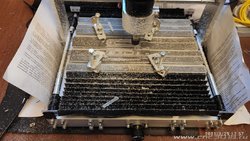
(К столу крепление забыл сфоткать). Посмотрим, как себя поведет. Но пока (после пластика) внутри все чисто. Снять и обслужить (смазать каретки) тоже легко.
Для оси Х (на портале) планирую использовать такой профиль:
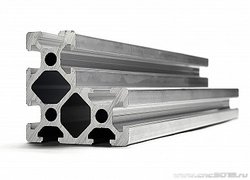
Профили использую соберизаводовские, т.к. рельсы mgn12ложатся на ребра, а не висят на краях паза.
Но вот теперь возникли вопросы. Самый первый: Ось Х будет делаться после оси Z. Захотелось попробовать шпиндель с водяным охлаждением, но они все от 800 Вт.Сможет ли родной движок таскать эту массу нормально, или оно повлечет изменение и этой части? Не хотелось бы из этого станка собирать полностью другой, но с недостатками этого. На форуме не нашел, но есть упоминания о том, что ставили такие (мое сообщение стерли в одной из тем, как не относящееся). Если есть, буду благодарен на ссылки на форуме/ютубе/просто текстом. Интересует так же шумность на 12-15 тыс. оборотах по сравнению с воздушником.
Второй. Если использовать шпиндель 800 Вт ф65 мм, это приведет к уменьшению рабочего поля по Х. Вот есть мысль, по краям (где крепятся стойки портала) к профилю 40х40 прикрутить профиль 40х20, и уже через него крепить стойки. Поле сохранится, а жесткость? Вероятно. Как думаете, стоит морочиться, или забить?